Short Term Corrosion Rate Formula
- Metal loss from the most recently or previous measured thickness
- LCR and SCR corrosion rates should be compared to see which results is the shortest remaining life as part of the data assessment. The corrosion rate with greater value should be selected for remaining life calculation of the piping system.
|
\( SCR \;=\; \dfrac{ t_i - t_a }{ TIT }\) (Short Term Corrosion Rate)
\( t_i \;=\; SCR \cdot TIT + t_a \)
\( t_a \;=\; t_i - SCR \cdot TIT \)
\( TIT \;=\; \dfrac{ t_i - t_a }{ SCR }\)
|
Symbol |
English |
Metric |
\( SCR \) = Short Term Corrosion Rate |
\( in \;/\; yr \) |
\( mm \;/\; yr \) |
\( t_i \) = Initial Thickness (Recently or Previous Measured Thickness) |
\( in \) |
\( mm \) |
\( t_a \) = Actual Thickness (Current Thickness) |
\( in\) |
\( mm \) |
\( TIT \) = Total Interval Exposure Time (Last or Interval Time - Actual Time) |
\( yr \) |
\( yr \) |
Corrosion rate, abbreviated as CR, is the speed at which a material deteriorates due to chemical reactions with its environment. It is typically measured in terms of thickness loss. Corrosion can affect various materials, including metals, polymers, ceramics, and composites.
Several Factors Influence the Corrosion Rate of a Material
Material Type - Different materials have varying susceptibilities to
corrosion.
Environmental Conditions - The presence of corrosive agents, such as moisture, oxygen, acids, and salts, can accelerate corrosion. The
temperature and humidity levels of the environment also play a role.
Mechanical Factors -
Stress,
strain, and mechanical wear can influence the rate of corrosion. Corrosion fatigue, for instance, occurs when a material is subjected to both corrosion and cyclic loading.
Electrochemical Factors - Many corrosion processes involve electrochemical reactions. The presence of an electrolyte (such as saltwater) can enhance the electrochemical reactions that lead to corrosion.
Protective Coatings - The presence of protective coatings, such as paint or corrosion inhibitors, can significantly reduce the corrosion rate by forming a barrier between the material and the corrosive environment.
pH Level - The pH of the environment can affect the corrosion rate. Some materials are more prone to corrosion in acidic or alkaline conditions.
Long Term Corrosion Rate Formula
- Metal loss from installation to when current thickness measurements were taken
- LCR and SCR corrosion rates should be compared to see which results is the shortest remaining life as part of the data assessment. The corrosion rate with greater value should be selected for remaining life calculation of the piping system.
|
\( LCR \;=\; \dfrac{ t_i - t_a }{ TET }\) (Long Term Corrosion Rate)
\( t_i \;=\; LCR \cdot TET + t_a \)
\( t_a \;=\; t_i - LCR \cdot TET \)
\( TET \;=\; \dfrac{ t_i - t_a }{ LCR } \)
|
Symbol |
English |
Metric |
\( LCR \) = Long Term Corrosion Rate |
\( in \;/\; yr \) |
\( mm \;/\; yr \) |
\( t_i \) = Initial Thickness (Installation Thickness) |
\( in \) |
\( mm \) |
\( t_a \) = Actual Thickness (Current Thickness) |
\( in \) |
\( mm \) |
\( TET \) = Total Exposure Time (Initial Time - Actual Time) |
\( yr \) |
\( yr \) |
To measure corrosion rates, various techniques are employed, including weight loss methods, corrosion coupons, electrochemical methods, and non-destructive testing techniques. It's crucial to manage and control corrosion in industries such as oil and gas, transportation, infrastructure, and manufacturing, as corrosion can lead to structural failures, increased maintenance costs, and safety hazards.
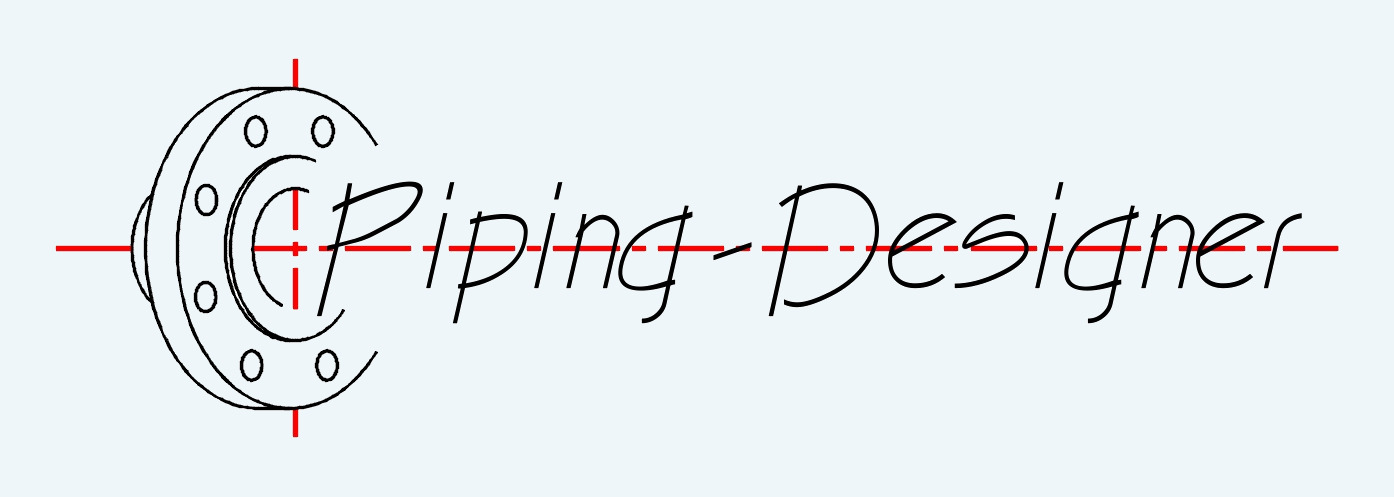
Remaining Life Determination Formula
|
\( RLD \;=\; \dfrac{ t_a - t_r }{ CR }\) (Remaining Life Determination)
\( t_i \;=\; RLD \cdot CR + t_a \)
\( t_a \;=\; t_i - RLD \cdot CR \)
\( CR \;=\; \dfrac{ t_i - t_a }{ RLD } \)
|
Symbol |
English |
Metric |
\( RLD \) = Remaining Life |
\( yrs \) |
\( yrs \) |
\( t_a \) = Actual Thickness (Current Thickness) |
\( in \) |
\(mm \) |
\( t_r \) = Thickness Required |
\( in \) |
\( mm \) |
\( CR \) = Corrosion Rate |
\( in \;/\; yr \) |
\( mm \;/\; yr \) |