Pressure vessel design pressure is the maximum internal pressure that the vessel is designed to handle during normal operation. It accounts for potential variations in operating pressure and ensures that the vessel can safely contain the process fluid under typical conditions. The design pressure is a crucial element in pressure vessel design, as it guides the selection of materials, wall thickness, and safety features.
Key Points about Design Pressure
Above Maximum Operating Pressure - The design pressure is typically set slightly above the maximum operating pressure of the system to ensure safety margins. For example, if a vessel operates at 150 psi, the design pressure might be set at 165 psi to account for potential fluctuations.
Determined by Process Conditions - Design pressure is determined based on the process fluid,
temperature, and expected pressure conditions during regular operation, including any pressure spikes or transient events.
Safety Factor - The design pressure includes a safety margin to ensure the vessel's structural integrity during normal and abnormal conditions. Typically, the design pressure is around 10% higher than the maximum expected pressure.
Applicable Standards - The design pressure is calculated following specific design codes and standards like:
- ASME Boiler and Pressure Vessel Code (BPVC), Section VIII
- EN 13445 (European Standard)
- BS 5500 (British Standard) These standards outline how to determine the design pressure based on material strength, temperature, and other safety factors.
Design Temperature - The
pressure rating is closely related to the design temperature. As temperature increases, the material strength may decrease, so the design pressure for high-temperature operations may be lower than for low-temperature operations.
Example of Design Pressure - If a pressure vessel operates at 500 psi, the design pressure might be set to 550 psi, allowing for some flexibility in case of pressure surges.
Factors Influencing Design Pressure
Fluid Type - The nature of the fluid (
gas,
liquid, corrosive material) affects the design pressure, as gases tend to exert more pressure than liquids, and corrosive materials require more robust materials.
Temperature - Higher temperatures reduce the strength of most materials, so a vessel designed to operate at high temperatures must account for this by having lower pressure ratings or using stronger materials.
Corrosion Allowance - If the vessel is exposed to corrosive materials, the design may incorporate thicker walls or corrosion-resistant materials to maintain the design pressure over time.
Internal and External Loads - Additional loads such as wind, seismic activity, and internal vacuum conditions may influence the vessel's design pressure.
Vessel Geometry - The shape of the pressure vessel (cylindrical, spherical, etc.) affects the
pressure distribution and must be considered in the design pressure calculation.
Typical Design Pressure Values
- Low-pressure vessels: 15-150 psi
- Medium-pressure vessels: 150-600 psi
- High-pressure vessels: 600-3,000 psi
- Ultra-high pressure vessels: Over 3,000 psi
Importance of Design Pressure
Design pressure is critical in ensuring the safety, reliability, and compliance of a pressure vessel. It prevents over-pressurization, which can lead to catastrophic failure, leaks, or explosions. Proper calculation of the design pressure also ensures that safety devices, like pressure relief valves, are correctly sized to handle excess pressure in emergency situations.
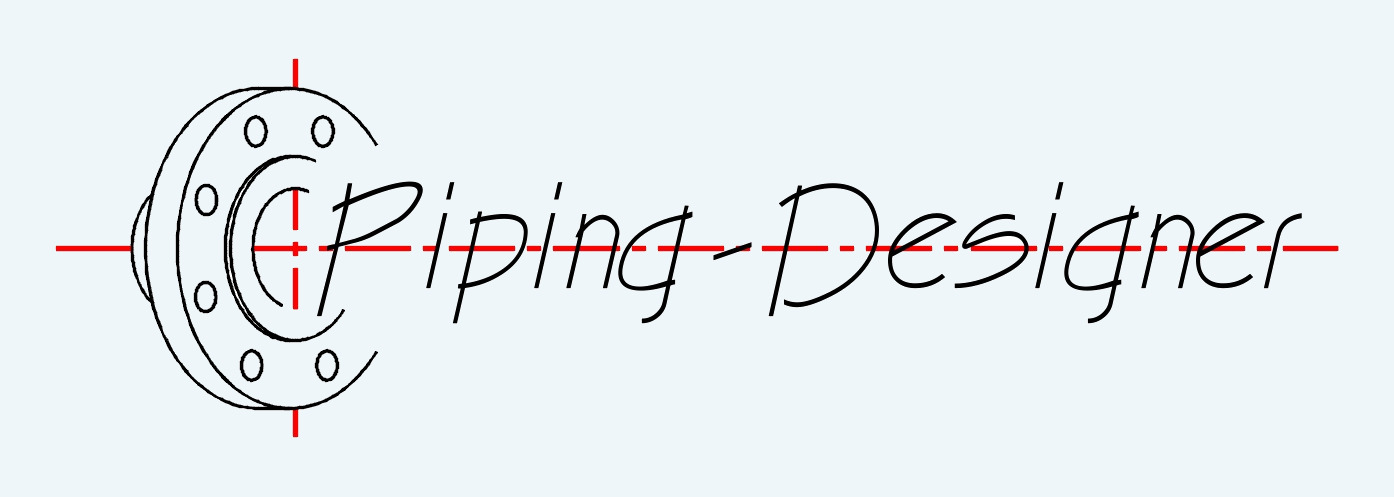