Fatigue Crack Growth
Fatigue crack growth is how cracks in a material propagate under repeated or cyclic loading. When a material is subjected to fluctuating stresses, such as those experienced by aircraft wings, bridges, or machinery, small imperfections or cracks can begin to form. Over time, these cracks grow incrementally with each stress cycle, even if the applied stress is below the material's ultimate strength. This process is distinct from sudden fracture because it occurs gradually, often over thousands or millions of cycles, making it a key concern in designing durable and safe structures.
The mechanism of fatigue crack growth typically unfolds in three stages. First, a crack initiates at a point of stress concentration, such as a surface defect, inclusion, or manufacturing flaw. In the second stage, known as stable crack growth, the crack advances steadily with each loading cycle. The rate of this growth depends on factors like the magnitude of stress, the material’s properties (toughness and ductility), and environmental conditions (temperature or corrosion). Engineers often use mathematical models, such as the Paris Law, to predict this growth rate, which relates the crack growth per cycle to the stress intensity factor at the crack tip. Finally, in the third stage, the crack reaches a critical size where the remaining material can no longer bear the load, leading to rapid, unstable fracture.
Understanding fatigue crack growth is essential for preventing catastrophic failures in real-world applications. Materials like metals, polymers, and composites all exhibit this behavior, though the specifics vary. For instance, ductile materials might show more resistance to crack growth due to plastic deformation, while brittle materials may fail more abruptly. Environmental factors, such as exposure to moisture or chemicals, can accelerate the process by introducing corrosion fatigue. To mitigate these risks, engineers employ strategies like regular inspections, material selection, and designing components to minimize stress concentrations, ensuring that structures can withstand the rigors of cyclic loading over their intended lifespan.
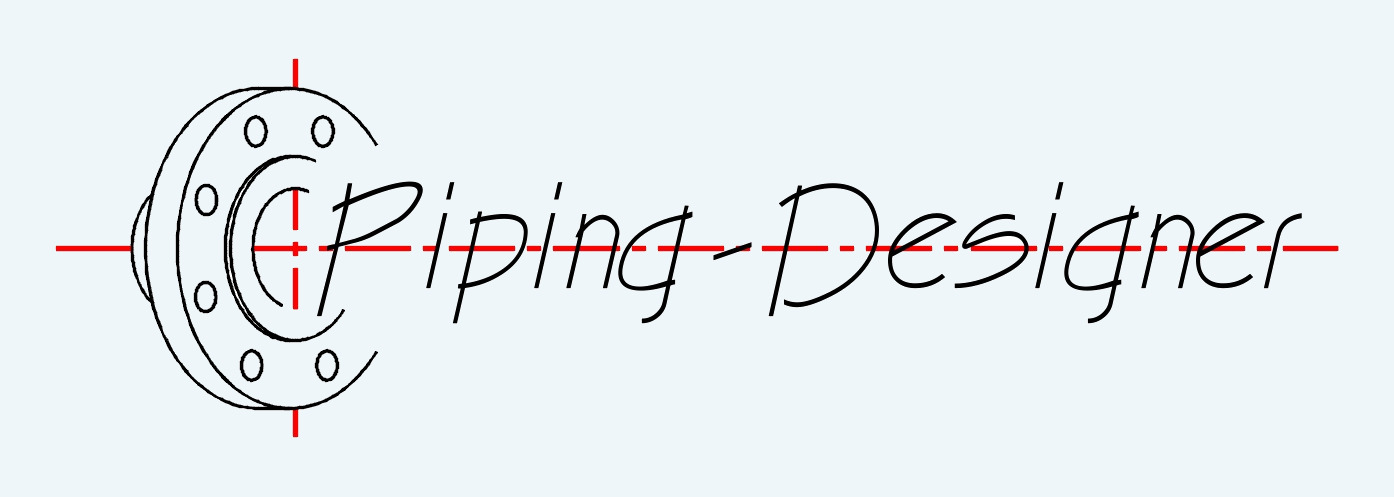