Galvanic Corrosion
Galvanic corrosion is an electrochemical process that occurs when two dissimilar metals come into electrical contact with each other in the presence of an electrolyte, such as water or saltwater. In this process, one metal (the more anodic metal) corrodes preferentially, while the other (the more cathodic metal) is protected from corrosion. The electrochemical potential difference between the two metals drives the flow of electrons, causing the anodic metal to lose electrons (oxidize) and degrade over time. The rate of galvanic corrosion depends on factors like the difference in electrode potential between the two metals, the conductivity of the electrolyte, and the relative surface areas of the metals in contact.
Some Factors Influencing Galvanic Corrosion
Electrode potential difference - Larger potential differences between the metals increase the rate of corrosion.
Area ratio - A large cathode and small anode increase corrosion at the anode.
Electrolyte properties - Conductive environments like seawater or moisture rich environments accelerate the corrosion process.
Prevention Methods
Protection against galvanic corrosion involves several strategies aimed at minimizing or preventing the electrochemical interaction between dissimilar metals. By implementing these strategies, galvanic corrosion can be minimized or eliminated, protecting the integrity of metal structures. Here are common methods used to prevent galvanic corrosion:
Use of Similar Metals - The most straightforward method is to use metals that are close to each other in the galvanic series (which ranks metals by their potential to corrode). The closer the metals are in the series, the less likely galvanic corrosion will occur.
Insulation and Coatings - One or both of the metals can be coated with non-conductive materials, like paint, powder coating, or plastic. This prevents direct contact and reduces the chance of galvanic corrosion. Use insulating materials (such as rubber, plastic, or gasket materials) between the two metals to prevent them from coming into direct electrical contact.
Cathodic Protection - Install a sacrificial anode, typically made from a more anodic metal like zinc or magnesium, which corrodes in place of the more critical metal. This is commonly used in pipelines, ships, and offshore structures. An external current can be applied to counteract the galvanic current, which prevents the more anodic metal from corroding.
Control of Environment - Reducing the presence of electrolytes, such as saltwater or moisture, can slow the galvanic process. This can be done by keeping surfaces dry or applying sealants. Ensure that areas where dissimilar metals are in contact do not trap water or other electrolytes, as this can accelerate corrosion.
Surface Area Control - If two metals must be in contact, design the system so that the anodic (less noble) metal has a larger surface area compared to the cathodic (more noble) metal. This reduces the rate of corrosion.
Anodic Metal Selection - Choose metals or alloys that are specifically designed to resist corrosion, such as stainless steel or alloys designed for marine environments.
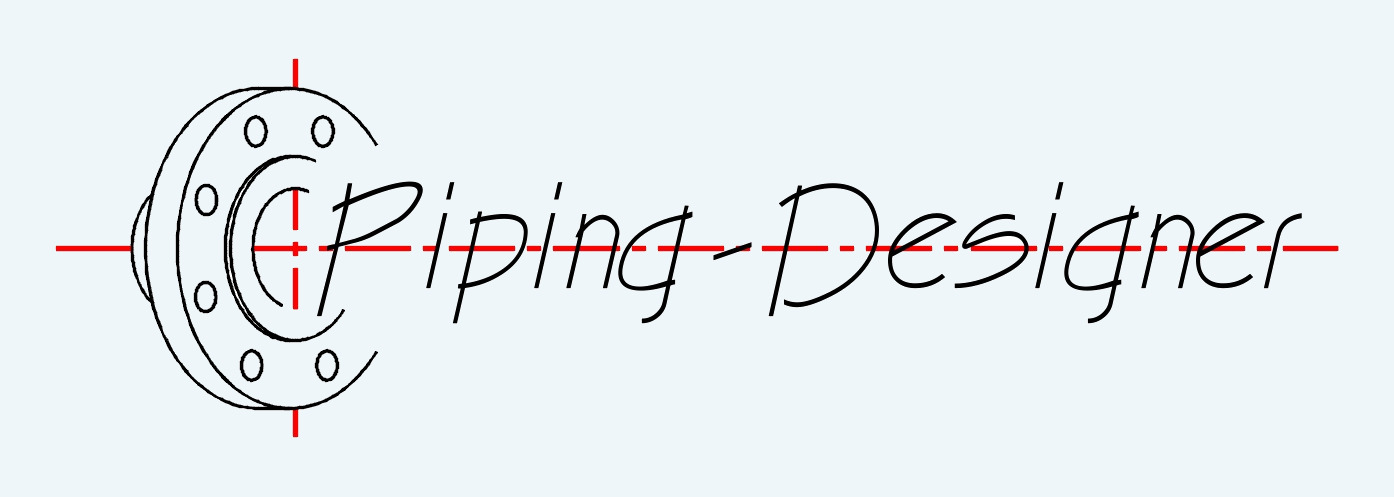