Wrought iron pipe, abbreviated as WIP, refers to a type of pipe made from wrought iron, which is a specific form of iron with a low carbon content. Wrought iron typically has a very low carbon content, generally less than 0.08%. The low carbon content is a distinguishing feature of wrought iron and contributes to its unique properties, such as toughness, malleability, and ductility. The process of making wrought iron involves working the iron at high temperatures and removing impurities, which helps maintain this low carbon content.
Wrought Iron Pipe Advantages and Disadvantages
|
Advantages | Disadvantages |
- Wrought iron is known for its durability and strength, making wrought iron pipes resistant to damage and corrosion.
- Properly maintained wrought iron pipes can have a long service life, especially when compared to certain other materials.
- Wrought iron has good fire resistance properties, providing a degree of fire safety in applications where this is a concern.
- Wrought iron has a distinctive appearance that some people find aesthetically pleasing, making it suitable for decorative or architectural applications.
- Wrought iron is relatively malleable, making it easier to work with and shape during manufacturing and installation.
|
- While wrought iron is more corrosion resistant than cast iron, it is still susceptible to rust and corrosion, especially in the presence of moisture. Regular maintenance, including painting, is often necessary to prevent corrosion.
- Wrought iron pipes are heavier than some alternative materials, which can make handling and installation more challenging.
- Wrought iron pipes can be more expensive than some modern materials like steel or PVC. The cost includes not only the material but also transportation and installation.
- Wrought iron pipes are not as readily available as some other materials due to the decline in their use over the years.
- Welding and joining wrought iron can be more challenging than with some other materials, and specialized skills and equipment may be required.
- Wrought iron pipes are largely obsolete in modern plumbing and construction due to the availability of more cost effective and corrosion resistant materials like steel and PVC.
- Wrought iron can be relatively brittle compared to materials like steel, and it may be more prone to cracking or breaking under certain conditions.
|
Production of Wrought Iron Pipe
The production of wrought iron pipes involves several steps, and it's important to note that the use of wrought iron pipes has diminished in modern times. However, historically, wrought iron pipes were produced for various applications such as water supply and gas transportation. The following are general steps involved in the production of wrought iron pipes:
Iron Smelting - Wrought iron is produced from pig iron, which is obtained by smelting iron ore in a blast furnace. The pig iron is then further refined to reduce its carbon content. The process involves oxidizing impurities and using a high-pressure blast of air.
Puddling - Puddling is a refining process used to further reduce the carbon content and other impurities in the iron. The pig iron is melted in a reverberatory furnace, and workers stir the molten iron while introducing oxidizing substances. This process helps to create a more malleable and fibrous wrought iron.
Wrought Iron Bar Production - The refined wrought iron is then typically cast into long bars or ingots. These bars are then worked, usually through rolling or forging, to achieve the desired shape and size. The repeated working of the iron helps align the fibrous structure and removes any remaining impurities.
Pipe Forming - Once the wrought iron bars are prepared, they can be shaped into pipes. This is often done through a combination of forging and rolling processes. The iron is heated and shaped using dies or molds to create the cylindrical form of a pipe.
Seam Welding - The pipes may be created by welding together the edges of a flat iron sheet or by welding a longitudinal seam along a forged or rolled piece. The welding process is essential for creating a continuous and leak-proof pipe.
Heat Treatment - The wrought iron pipes may undergo heat treatment processes to improve their mechanical properties, such as strength and toughness.
Surface Treatment - The pipes may be coated or treated to improve their corrosion resistance. This could involve applying a protective coating or using a galvanization process.
It's important to highlight that the production of wrought iron pipes has become less common due to the availability of materials with better corrosion resistance and other improved properties, such as steel and various types of plastics. Modern pipes are typically made from materials that offer better performance, durability, and cost effectiveness in comparison to traditional wrought iron pipes.
Uses for Wrought Iron Pipes
Wrought iron pipes were historically used for various purposes, particularly in water supply and transportation of gases. However, it's important to note that the use of wrought iron pipes has declined significantly in modern times due to the availability of more corrosion resistant materials like steel and various types of plastic.
Water Supply Systems - Wrought iron pipes were commonly used for water supply systems in the past. They were employed for the distribution of potable water in cities and towns.
Gas Pipelines - Wrought iron pipes were also used for the transportation of gas. However, due to the potential for corrosion, modern gas pipelines are typically made from materials like steel or plastic.
Industrial Applications - In certain industrial settings, wrought iron pipes may have been used for transporting fluids, although this usage has diminished with the adoption of more corrosion resistant materials.
Plumbing - Wrought iron pipes were historically used for plumbing applications. However, as mentioned earlier, modern plumbing systems often use materials like copper, PVC, or steel.
Historical Restoration - In cases where historical accuracy is essential, wrought iron pipes might be used in the restoration of older buildings or infrastructure to maintain authenticity.
It's crucial to recognize that the use of wrought iron pipes has diminished due to certain limitations, including susceptibility to corrosion and the availability of more durable and cost effective materials. In modern construction and infrastructure projects, materials like steel, stainless steel, copper, and various types of plastics are more commonly used for pipes and pipelines. If you are considering the use of pipes in a contemporary context, it's advisable to consult with a professional engineer or plumber to determine the most suitable and code compliant materials for your specific application.
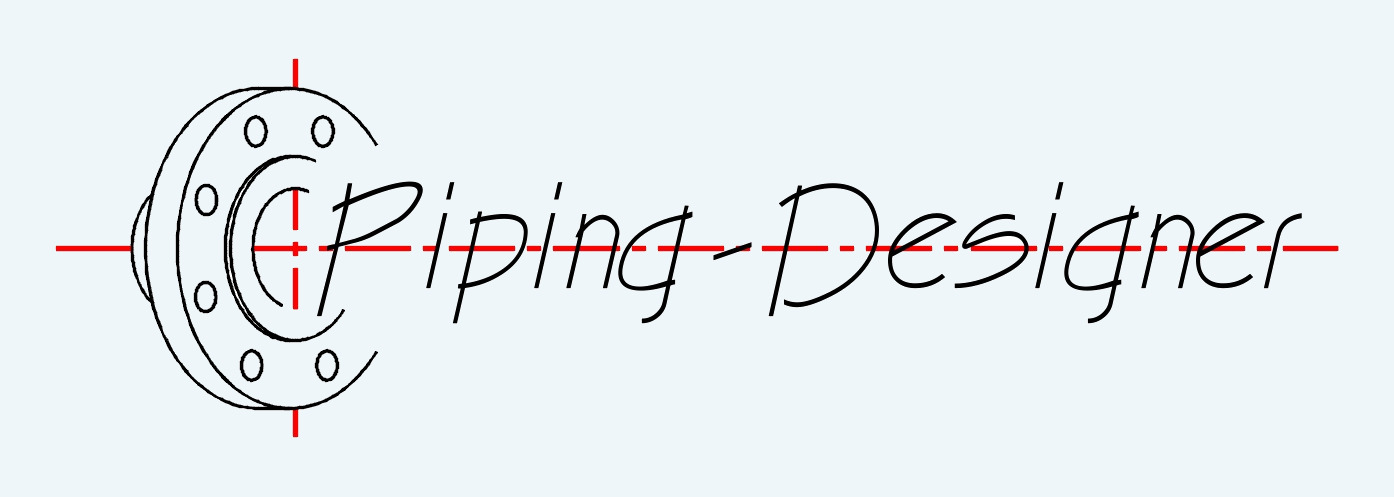