Pressure Vessel Pressure Rating
Pressure vessel pressure ratings define the maximum internal pressure that a vessel can safely contain without risk of failure. These ratings are determined based on various factors, including the material strength, wall thickness, design temperature, and type of fluid contained within the vessel. Pressure vessels are used in many industries (chemical, petrochemical, oil and gas, power generation), so adhering to the correct pressure ratings is crucial for safety and compliance. By combining these factors, engineers can determine the appropriate pressure ratings and ensure safe operation of pressure vessels.
Key Points about Pressure Ratings
Design Pressure - The maximum pressure that the vessel is designed to withstand during normal operation. It's usually slightly higher than the vessel's maximum operating pressure to account for potential variations.
Maximum Allowable Working Pressure (MAWP) - The maximum pressure at which the weakest part of the vessel can operate at its design temperature. This is a critical figure and must not be exceeded to ensure safety.
Hydrostatic Test Pressure - The pressure used to test the vessel for leaks and structural integrity, typically 1.3 to 1.5 times the MAWP.
Operating Pressure - The typical pressure that the vessel operates at during regular service, usually below the design pressure.
Design Temperature - This impacts the pressure rating because materials behave differently at varying temperatures. For example, metals may lose strength at elevated temperatures, affecting the MAWP.
Code Compliance - Pressure vessels are designed following various codes and standards, the most common being the ASME Boiler and Pressure Vessel Code (BPVC). ASME Section VIII specifies design, construction, testing, and inspection criteria for pressure vessels in the U.S.
Material - The type of material (steel, aluminum, composite, etc.) influences the pressure rating because each material has specific strength limits.
Corrosion Allowance - A vessel exposed to corrosive substances may have a higher safety factor or thicker walls to compensate for material loss over time.
Joint Efficiency - The quality of welded joints can impact the pressure rating, as weaker joints can reduce the overall strength of the vessel.
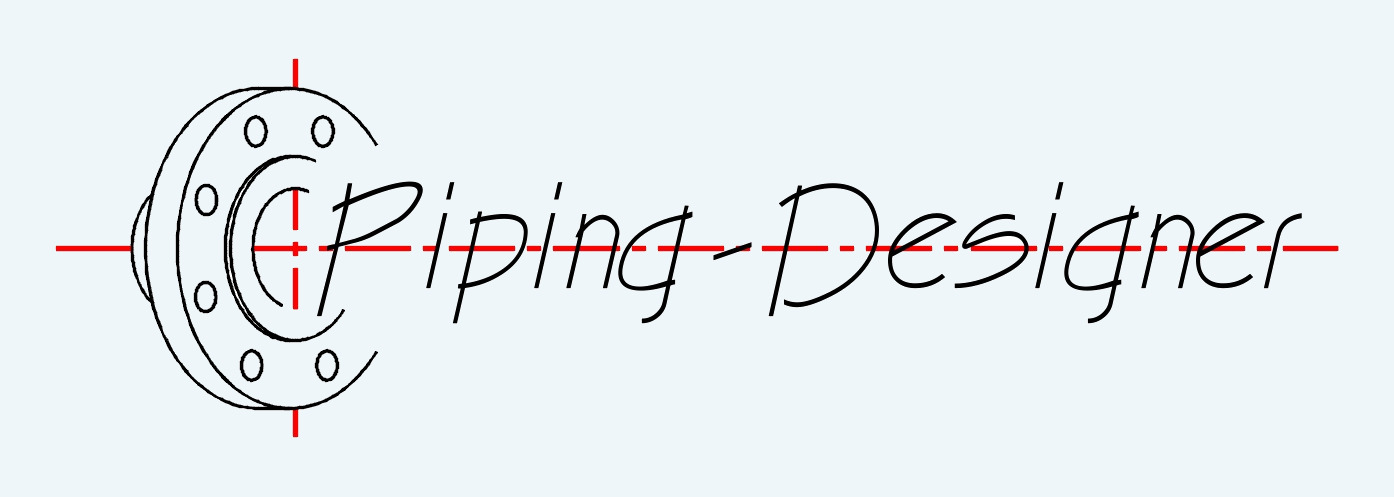