DC Motor Armature Voltage
DC Motor Armature Voltage Formula |
||
\( V_a \;=\; E_b + I_g \cdot R_a \) (DC Motor Armature Voltage) \( E_b \;=\; V_a - I_g \cdot R_a \) \( I_g \;=\; \dfrac{ V_a - E_b }{ R_a }\) \( R_a \;=\; \dfrac{ V_a - E_b }{ I_g }\) |
||
Symbol | English | Metric |
\( V_a \) = Armature Voltage | \(V\) | \(V\) |
\( E_b \) = Back EMF | \(V\) | \(V\) |
\( I_a \) = Armature Current | \(I\) | \(I\) |
\( R_a \) = Armature Resistance | \(\Omega\) | \(\Omega\) |
DC motor armature voltage is the voltage applied across the armature (the rotating part) of a direct current (DC) motor. The armature is typically a coil of wire wound around a core that sits within a magnetic field created by the motor's field windings or permanent magnets. This voltage is used to determining the motor's performance, including its speed and torque.
It causes current to flow through the armature resistance, producing a magnetic field that interacts with the stator's magnetic field to generate rotational motion. It also counteracts the back electromotive force induced in the armature due to its rotation in the magnetic field. In a DC motor, the speed is largely influenced by the armature voltage. Increasing typically increases the motor speed, assuming a constant load, because (and thus speed) adjusts to balance the equation. Armature voltage is controlled using external circuits like variable resistors, choppers, or pulse-width modulation in modern systems to regulate motor behavior.
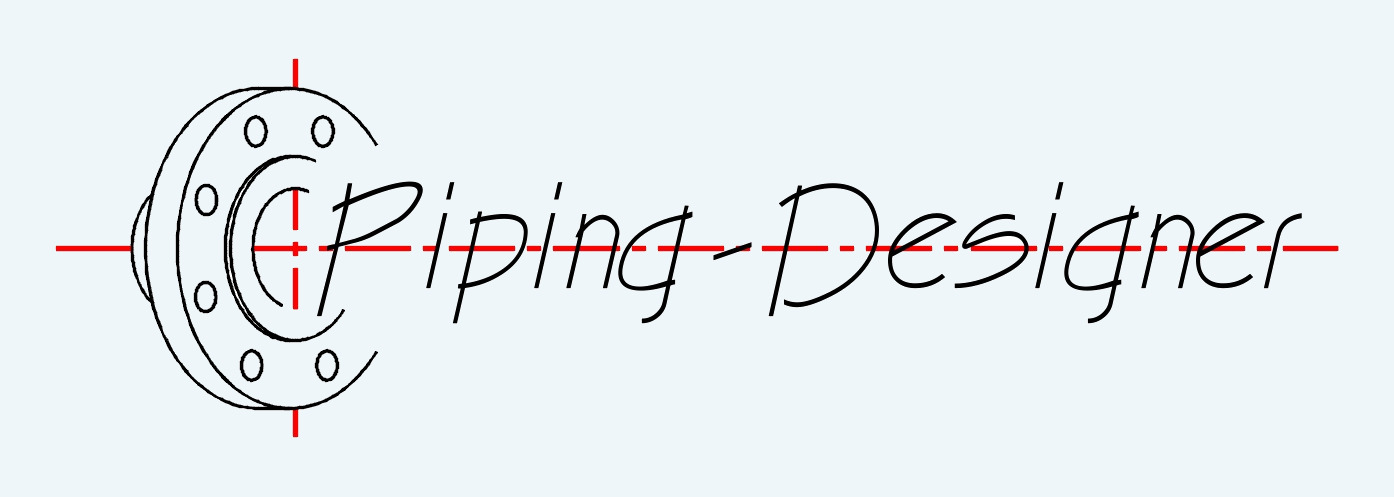
DC Motor Armature Voltage Formula
|
||
\( V_a \;=\; K_a \cdot n \cdot \Phi_B \) (DC Motor Armature Voltage) \( K_a \;=\; \dfrac{ V_a }{ n \cdot \Phi_B }\) \( n \;=\; \dfrac{ V_a }{ K_a \cdot \Phi_B }\) \( \Phi_B \;=\; \dfrac{ V_a }{ K_a \cdot n }\) |
||
Symbol | English | Metric |
\( V_a \) = Armature Voltage | \(V\) | \(V\) |
\( K_a \) = Motor Constant (Depends on the Design) | - | - |
\( n \) = Motor Speed | \(RPM\) | \(RPM\) |
\( \Phi_B \) (Greek symbol Phi) = Armature Magnetic Flux | \(V\;/\;sec\) | \(Wb \;/\; mm^2\) |