Corrosion Engineering
Pipeline Pigging, Cathodic Protection, EngineeringCorrosion engineering is a branch of engineering that focuses on preventing and controlling the deterioration of materials due to chemical reactions with their environment. Corrosion is a major problem in many industries, including oil and gas, chemical processing, and transportation, as it can lead to equipment failure, safety hazards, and environmental damage. The work of a corrosion engineer typically involves identifying the causes and mechanisms of corrosion, selecting appropriate materials and coatings to prevent corrosion, and developing strategies to control and mitigate the effects of corrosion. They use a variety of tools and techniques to analyze the properties and behavior of materials in different environments, such as electrochemical testing, material characterization, and computational modeling.
Engineering |
Chemical Engineering |
Corrosion engineers work in a variety of industries and settings, including research and development, design and construction, and maintenance and repair. They may work on projects related to pipeline integrity, oil rig maintenance, or material selection for chemical processing equipment. In addition to preventing and controlling corrosion, corrosion engineers may also work on projects related to material testing and certification, environmental monitoring and remediation, and safety and risk assessment. They often collaborate with other engineers, scientists, and technicians to develop and implement effective corrosion management strategies.
These engineering is a critical field that plays an important role in many industries. By preventing and controlling the effects of corrosion, corrosion engineers help to ensure that industrial processes operate safely and efficiently, while also minimizing environmental impact and protecting public health and safety.
- See Articles - List of Tags / List of Categories / List of Articles / List of Glossaries / Nomenclature and Symbols / (See Corrosion Glossary)
Corrosion Types
- Cavitation - Corrosion gas bubble formation & immediate collapse. The erosion is caused by the relative movement between a corrosive fluid and a metal surface. Localized cavities of vapor form on the low pressure side of the pump (suction) and collapse on themselves as energy is added to the fluid.
- Corrosion Erosion - Velocity aggravated corrosion. Caused by the rapid flow of any turbulent liquid through the piping. The rate of corrosion is dependent on the level of turbulance.
- Corrosion Fatigue - Corrosion on cyclic loads. Stress corrosion cracks occur due to the effecte of static stress. The applied stresses are cyclic as a result of mechanical or thermal effects.
- Crevice - Portion of the surface is isolated from the environment. The presence of small volumes of stagnant solution beneath deposits and seals, or in crevices, at nuts and rivet heads. Deposits of sand, dust, scale and corrosion products can all create zones where the liquid can only be renewed with great difficulty.
- Galvanic Corrosion - Caused by dissimilar metals. An electrochemical process whereby one metal corrodes when in contact with another metal through an electrolyte. During this process, one metal can experience severe corrosion, while the other remains relatively unaffected.
- Intergranular - Corrosion at the grain boundaries. It happens along the crystal boundary of the metal when exposed to certain corrosive medium. The corrosion starts from the surface, develops into the inside of the metal along the crystal boundary until it collapses devoid of all the metal strength. It happens even when the surface looks fine but actually the grains inside the metal have lost the binding force and the metal sound.
- Pitting - Localized on metal surface. A localized form of corrosion which is characterized by small holes forming in materials, most often metal piping. While these pits may be small on the surface, they can be larger underneath, potentially being more damaging than they appear.
- Selective Leaching - Only one metal in an alloy is attacked. in some solid solution alloys, when in suitable conditions a component of the alloys is preferentially leached from the material. The less noble metal is removed from the alloy by a microscopic-scale galvanic corrosion mechanism. The most susceptible alloys are the ones containing metals with high distance between each other in the galvanic series.
- Stress Corrosion Cracking - When a susceptible material is exposed to a contaminant that concentrates in an area affected by tensile stresses in excess of its threshold.
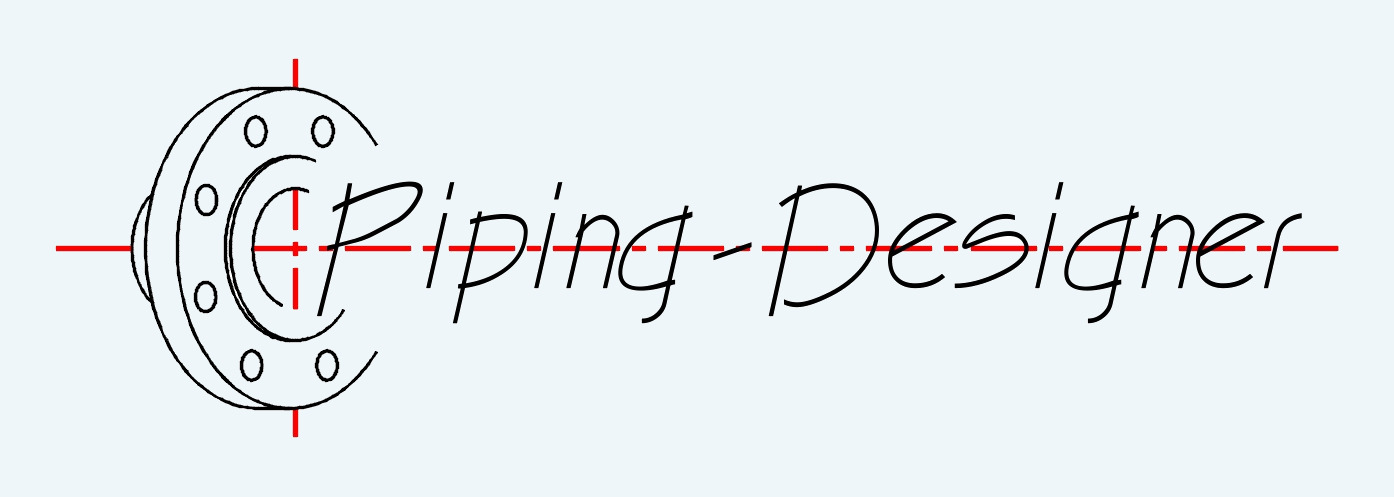