Butterfly Valve Datasheets
Face to face dimensions for full and standard port valves is the same. All ball valves 2" and below are both standard and full port valves. |
Butterfly Type | Datasheets | Butterfly Type | Datasheets |
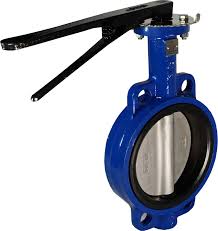 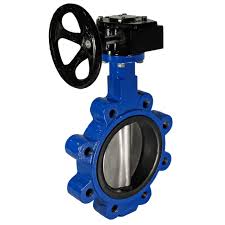 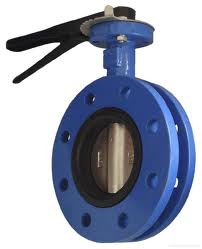 |
- Butterfly Valves, Wafer, Lug, Flange
|
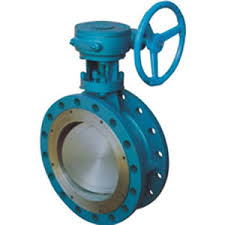 |
- Butterfly Valves, Triple-offset
|
A butterfly valve, abbreviated as BTFLV, is a quarter turn valve (90° or less) with a circular disk as its closing element. The standard design has the valve stem running through the disk, giving a symmetrical appearance. Other designs offset the stem. Advantages include less wear and tear on the disk and seats, and tighter shut-off capabilities. When space is limited, sometimes larger valves may use a hand wheel with a gear arrangement. Butterfly valves are rather easy to maintain. These valves are used for gases, liquids, slurries, powders, and vacuum.
There are Two Butterfly Valve Categories
Category A - Manufacturer's rated cold working pressure (CWP) butterfly valves, usually with a concentric disc and seat configuration. Sizes covered are NPS 2 to NPS 48 for valves having ASME Class 125 or Class 150 flange bolting patterns.
Category B - Pressure-temperature rated butterfly valves that have an offset seat and either an eccentric or a concentric disc configuration. These valves may have a seat rating less than the body rating. Sizes covered are NPS 3 to NPS 24 for Classes 150, 300, and 600.
Butterfly Valve Design Classification
Double Offset Butterfly Valve - This valve features the stem center deviated from the center of the disc and valve. With this structure, the valve disc can leave the valve seat quickly, greatly reducing unnecessary over compression and scraping between them. This structure also helps decrease the wearing process and prolongs the operational life of the valve.
Fire Tight Valve - When using valves in a service that may provide fuel to a fire, it is important to ensure that they are fire tight. Typically the seat in a soft seated fire tight valve contains a metal strip that will provide additional sealing should the seat be burnt or melted away. Fire tight valves can be found on fuel gas applications, VRU systems and in other flammable systems.
Flange Style Butterfly Valve - A butterfly valve with a flange on each end. These have a larger face to face dimension than the wafer and lug style butterfly valves and should not be used when there is limited space. These valves connect directly to the flanges by means of machine bolt to each side of the valve. If the valve torque is high or valve operations become too frequen, a manual flanged butterfly valves can be automated if need be.
High Performance Butterfly Valve - A valve in which the stem is not collinear to the disc centerline but rather offset from the center. The use of offset design helps to enhance uniform tight shut-off against the valve seat and also reduce wear due to friction. This valve can be used for shut-off and throttling fluid flow applications. This valve is made to handle different fluids from general fluid flow applications to viscous and corrosive fluids. The corrosive fluids can be gases or steam. High-performance butterfly valves are mostly of large sizes like 60 inch diameter.
Lug Style Butterfly Valve - Lug butterfly valves connect directly to the flanges by means of a lug or machine bolt. Since these are attached directly to the flanges, each length of pipe on either side of hte valve can be removed and replaced independant of the other. Unlike a wafer type butterfly valve, a lug style valve can serve as an end of the line valve. Lug style butterfly valves have the same face to face dimensions as a wafer style butterfly valve. The valves can be used for end of line service but a blind flange is always recommended. The valves are manufactured to be compatible with either pneumatic or electric actuation.
Triple Offset Butterfly Valve - The design eliminates the rubbing between the seat and seal ring through the flow path, reducing seat and seal wear and extending cycle life. They are used in applications similar to gate valves, where a metal seat is required, and tight shutoff and/or quarter-turn actuation is desired. Triple offset butterfly valves can open and close more quickly and can be frequently operated, even if there is an emergency shutoff. This valve has low torque and is recommended for both high and low temperature applications.
Wafer Style Butterfly Valve - Most wafer style butterfly valves are engineered with four holes that align with the connected pipeline. The valve is sandwiched between two flanges. The rubber valve seat creates a strong seal between the valve and flange connection. Unlike lug style butterfly valves, wafer style butterfly valves cannot be used as pipe ends or end of line service. The entire line must be shut down if either side of the valve requires maintenance. Wafer style butterfly valves are manufactured to be compatible with either pneumatic or electric actuation. Disc and seat material should be determined based on application and flow media.
Zero Offset Butterfly Valve - Concentric or rubber seated are other names for the zero-offset design. Zero offset means there is no offset by the stem of the valve. The valve seals via interference along the disc edge at the stem between the disc and the rubber seat.
-
Engineering Glossary
- A - B - C - D - E - F - G - H - I - J - K - L - M - N - O - P - Q - R - S - T - U - V - W - X - Y - Z
- Acoustical Engineer - The science of sound and vibrations, or anything related to the organs used to preceive sound.
- Aeronautical Engineer - Concerned with design, developement, testing, and production of aircraft, spacecraft, and related systems and equipment.
- Agricultural Engineer - Improves processes associated with managing natural resources and producion by develope methods to conserve soil and water, improve food production, and designing agricultural equipment.
- Architectural Engineer - Works in the design of one or more of the building systems such as structural, acoustical systems, HVAC systems, electrical, lighting, and plumbing,
- Automation Engineer - Design, develope, and test automated machines and processes.
- Automotive Engineer - Involves a combination of different engineering fields, which are applied in the design, developement and production of automotive vehicles like buses, cars, mopeds, motorbikes, and vans.
- A - B - C - D - E - F - G - H - I - J - K - L - M - N - O - P - Q - R - S - T - U - V - W - X - Y - Z
- Biochemical - Work with cells, enzymes, and antibodies to collect data, explore medical possibilities, and solve biological issues.
- Bioengineering Engineer - Solves problems in biology, medicine, health care and other fields.
- Biological Engineer - Studies the environment to improve the way we conserve soil, water and natural resources.
- Biomechanical Engineer - Designs new medical devices such as artificial organs and diagnostic equipment. They may also wotk in clinics, hospitals, oand doctors offices instslling and maintaining medical equipment.
- Biomedical Engineer - Is the developement of devices, and procedures that solve medical and health-related problems by combining a knowledge of biology and medicine with engineering principles and practices.
- Biotechnology - Involves the design, developement, and application of innovative technologies, products and/or environmentally sustainable systems through the efficient use of biological resources.
- A - B - C - D - E - F - G - H - I - J - K - L - M - N - O - P - Q - R - S - T - U - V - W - X - Y - Z
- Ceramic Engineer - Deals with the design, manufacturing, properties, and use of ceramic related things.
- Chemical Engineer - They invent, develope, design, operate, and manage processes that meet society's needs
- Civil Engineer - Oversee large construction projects, including designing, constructing, supervising, and maintaining road systems and the accompanying infrastructure, buildings, airports, and systems of water treatment, hydroelectricity, etc.
- Coastal Engineer - Also called Marine engineer. TIs the study of the processes ongoing at the shoreline and construction within the coastal zone.
- Communication Engineer - They are responsible for the planning, analysis and design, implementation, operation, testing, maintenance and management of communication systems and distributed information systems.
- Construction Engineer - Focuses on the design and construction processes required to produce facilities and systems that are essential to modern life and infrastucture.
- Corrosion Engineer - Responsible for analyzing engineered materials and coming up with the strategies for slowing or haulting the effects of corrosion.
- Cyber Security Engineer - Responsible for testing and screening security software and for monitoring networks and systems for security breaches or intrusions.
- A - B - C - D - E - F - G - H - I - J - K - L - M - N - O - P - Q - R - S - T - U - V - W - X - Y - Z
- Data Analytics Engineer - Responsible for finding trends in data sets and developing algorithns to help make raw data more useful to the end-user.
- A - B - C - D - E - F - G - H - I - J - K - L - M - N - O - P - Q - R - S - T - U - V - W - X - Y - Z
- Electrical Engineer - Involved in designing, developing, and supervising the manufacture of electrical equipment, such as electric motors, radar and navigation systems, power generation equipment or communication systems.
- Environmental Engineer - Works to improve water and air pollution, public health, and water disposal by using principles of engineering chemistry, biology, and soil science to develope solutions to environmental problems such as unsafe drinking water or climate change.
- A - B - C - D - E - F - G - H - I - J - K - L - M - N - O - P - Q - R - S - T - U - V - W - X - Y - Z
- Fire Protection Engineer - Responsible for designing and implementing solutions to lower fire risks to buildings and properties.
- Forensic Engineer - They investigate the materials, products, structures or components that fail or do not operate or function as intended, causing personal injury or damage to property.
- Forest Engineer - Is the management of forest lands including roads, planning forest harvesting, land environmental requirements, soils, watersheads, protection of wildlife and fish habitats.
- A - B - C - D - E - F - G - H - I - J - K - L - M - N - O - P - Q - R - S - T - U - V - W - X - Y - Z
- Geotechnical Engineer - The disciplines focuses on the behavior of earth materials, such as soil, rock, and groundwater, and their interaction with structures built on or in them. Geotechnical engineers use their knowledge of the physical and mechanical properties of soil and rock to design and construct safe and stable structures, such as buildings, roads, bridges, tunnels, dams, and levees.
- A - B - C - D - E - F - G - H - I - J - K - L - M - N - O - P - Q - R - S - T - U - V - W - X - Y - Z
- Hydrological Engineer - Also called Water Resources engineer or Hydrologist. It is concerned with the flow, treatment, and storage of water.
- A - B - C - D - E - F - G - H - I - J - K - L - M - N - O - P - Q - R - S - T - U - V - W - X - Y - Z
- Industrial Engineer - Work in planning, designing, implementing and controlling the system that enable people to use technology to find ways to eliminate wastefulness in production processes.
- Logistics Engineer - Develope solutions to improve the efficiency of product acquisition, distribution, storage, transportation, and warehousing.
- A - B - C - D - E - F - G - H - I - J - K - L - M - N - O - P - Q - R - S - T - U - V - W - X - Y - Z
- Maintenance Engineer - Oversees the installation, maintenance, and repair of heavy machinery, plant equipment, tools, and systems used in manufacturing.
- Manufacturing Engineer - This disciplines focuses on the design, integration, or improvment of manufacturing systems or related processes.
- Marine Engineer - Also called Coastal engineer. Designs, develops, and is responsible for the installation of ship machinery and related equipment.
- Materials Science Engineer - Societies want new and improved materials with more capabilities. These engineers have studied the properties and behavior of materials to create new ceramics, metals, and polymers.
- Mechanical Engineer - This is the most diverse of the engineering disciplines and can cross over into aerospace, automotive, construction, electronics, petroleumand manufacturing. These engineers design, develope, install, test, and maintain equipment or systems.
- Mechatronics, Robotics, and Automation Engineer - This is a combination of computer, electrical, and mechanical engineering.
- Metallurgical Engineer - Deals with extracting and processing of metals. They examine the performance of metals, and determine which ones can be put to uses to produce useful product.
- Mining Engineer - Find, develope, and recover the resources needed to support the needs of society from the minerals used for buildings, computers, roads, and other daily used items.
- A - B - C - D - E - F - G - H - I - J - K - L - M - N - O - P - Q - R - S - T - U - V - W - X - Y - Z
- Nuclear Engineer - Involved in the research and developement of the instruments, processes, and systems used in order to gain the benifits of radiation and nuclear energy.
- A - B - C - D - E - F - G - H - I - J - K - L - M - N - O - P - Q - R - S - T - U - V - W - X - Y - Z
- Petrochemical Engineer - Deals with the chemical processes involved in turning the raw materials of crude oil and petroleum into useful products such as clothes, fertilizers, food, and plastics.
- Petroleum Engineer - Designs, developes, and improves ways to get gas and oil deposits from below the ground's surface.
- Pharmaceutical Engineer - These professionals change raw materials into usefull products by using chemical and physical properties.
- Photonics Engineer - They research, design, and develope a wide range of technologies which utilize light energy.
- Plastics Engineer - Has knowledge of different types of plastic materials and their common uses. They design, process, and manufacture plastics that can withstand temperature and weather changes, resist corrosion, and exhibit electrical properties.
- Plumbing Engineer - Works on project designs, including analyzing the building, performing design calculations, and choosing the appropriate plumbing system, equipment and installation.
- Polymer Engineer - An engineer with understanding in both the properties and processing methods of polymer materials such as molding materials, plastics, rubbers, synthetic fibers, and more.
- Process Engineer - They are employed in many different industries such as agriculture, chemistry, geology, forestry, and nuclear. Their job is to work with scientists in research and developement, improve products and the product process.
- A - B - C - D - E - F - G - H - I - J - K - L - M - N - O - P - Q - R - S - T - U - V - W - X - Y - Z
- Reservoir Engineer - Focuses on optimizing the fluid flow of petroleum oil and gas reserves using special tools and equipment, continuously monitoring the reserve during the drilling proess, and analyzing the flow of each reserve to ensure efficiency.
- A - B - C - D - E - F - G - H - I - J - K - L - M - N - O - P - Q - R - S - T - U - V - W - X - Y - Z
- Structural Engineer - They ensure that specific components such as beams, columns, and foundations are structurally sound, where civil engineers do the designing.
- Surveying Engineer - Their work involves legal boundaries, record results, elevation and GPS, drainage systems, subdivision planning and layout, and topographical mapping.
- Systems Engineer - Identifies a problem and developes a solution that is constantly reevaluated throught its execution. Lays the foundation for effective planning and production, improve system reliavility, planning and executing, system maintainability and availability.
- A - B - C - D - E - F - G - H - I - J - K - L - M - N - O - P - Q - R - S - T - U - V - W - X - Y - Z
- Telecommunication Engineer - Provides a range of engineering solutions for satellite transmission, fiber-optics, analog and digital communications, network management, data analysis, circuits, programming language, technical wiring, and computer networks.
- Transportation Engineer - Applies engineering design, principles, and maintenance to roads, railways, waterways and more. This can include automotive technology, construction methods, ecconomics of design, land developement, mass transit systems, planning, probability, safety analysis, traffic flow.
- A - B - C - D - E - F - G - H - I - J - K - L - M - N - O - P - Q - R - S - T - U - V - W - X - Y - Z
- Waste Management Engineer - A series of technologies and services (infrastructure) for the collection, containment, transport, treatment, and management of waste, particularly human waste and wastewater. It comprises waste products that travel through infrastructure that employ various sensitive technologies that are specific to the type of waste and the local sanitation requirements.
- Water Resources Engineer - Also called a Hydrological engineer. They are involved in analysis, coastal protection, flood control, river management, soil physics, urban drainage, water cycle management, wastewater treatment, water flow, and water storage.
- Welding Engineer - These engineers have knowledge more than just welding, they also have a background in math, science, general engineering, materials, thermodynamics, welding design, and welding processes.
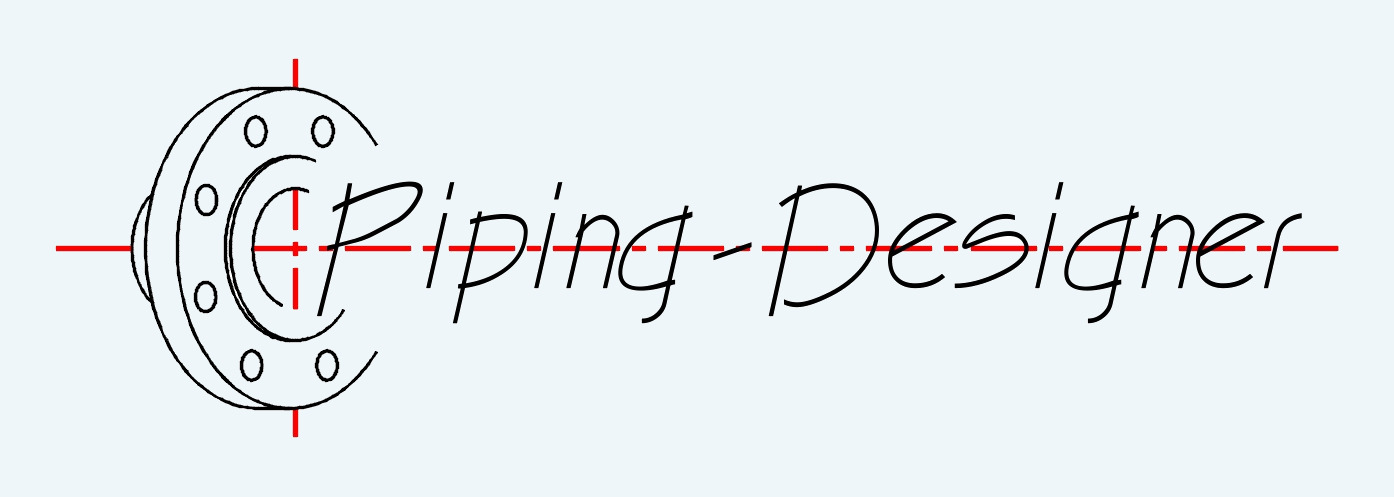
Read more
-
Mathematics Glossary
- A - B - C - D - E - F - G - H - I - J - K - L - M - N - O - P - Q - R - S - T - U - V - W - X - Y - Z
- Algebra - Uses letters or symbols as a place holder for unknown values or numbers. These variables are used to represent relationships and to solve equations.
- Analysis - The approximation of certain mathematical objects, like numbers or fractions.
- Applied Mathematics - Applies programs that typically involve a wider range of study to problems that arise in various areas.
- Arithmetic - The study of numbers and the properties of their operations.
- A - B - C - D - E - F - G - H - I - J - K - L - M - N - O - P - Q - R - S - T - U - V - W - X - Y - Z
- Biomathematics - The mathematical way to study biology and medicine.
- A - B - C - D - E - F - G - H - I - J - K - L - M - N - O - P - Q - R - S - T - U - V - W - X - Y - Z
- Calculate - Determines the amount or number of something using mathematical methods.
- Calculus - The study of how things change.
- Chaos Theory - Deals with complex systems whose behavior is highly sensitive to slight change in conditions.
- Combinatorics - Concerned with the number of ways of choosing some objects out of a collection.
- Computation - A calculation that includes borh arithmetical and non-arithmetical steps and follows a defined method.
- Computational Statistics - The interface between statistics and computer science.
- Constant - Something continuing forever or for an indefinitely long time.
- Continuous - Deals with connected objects. Connected objects are those which are not seperated from each other, such as set of real numbers.
- Cryptography - The secret writing with the intention fo keeping the data secret.
- Counting - The action of finding the number of elements of a finite set of objects.
- A - B - C - D - E - F - G - H - I - J - K - L - M - N - O - P - Q - R - S - T - U - V - W - X - Y - Z
- Derivative - A derivative is a basic tool of calculus. It is a variable that measures the rate of change of the function value (output value) with respect to a change in its argument (input value). Example: acceleration is the rate of change of velocity, therefore, acceleration is the derivative of velocity.
- Discrete Mathematics - Deals with discrete objects. Discrete objects are those which are seperated from each other, such as set of integers.
- Dynamical Systems - How the state of a system changes with time.
- A - B - C - D - E - F - G - H - I - J - K - L - M - N - O - P - Q - R - S - T - U - V - W - X - Y - Z
- Elementary Algebra - Performs basic concepts of algebra operations.
- Equation - A statement containing one or more variables that are either added, subtracted, divided, or multiplied to get an answer or a value.
- Estimate - An approximate calculation of a quantity.
- Estimation - The process of finding an approximation.
- Euclidean Geometry - The study of plane and solid figures.
- A - B - C - D - E - F - G - H - I - J - K - L - M - N - O - P - Q - R - S - T - U - V - W - X - Y - Z
- Finite - Something that is bounded or limited in magnitude or special or temporal extent.
- Formula - A rule expressed in symbols or a concise way of expressing information.
- A - B - C - D - E - F - G - H - I - J - K - L - M - N - O - P - Q - R - S - T - U - V - W - X - Y - Z
- Game Theory - The social interactions, which attempts to explain the mathematical conflicts, cooperation, and interactions people have with one another.
- Geo-statistics - The study of spiral or spatiotemporal datasets.
- Geometry - Deals with shapes and their properties or relationships to circles, lines, points, etc. These relationships can be expressed in plane geometry, two-dimensional figures and solid geometry, three-dimensional figures.
- Group Theory - The study of a set of elements present in a group.
- A - B - C - D - E - F - G - H - I - J - K - L - M - N - O - P - Q - R - S - T - U - V - W - X - Y - Z
- Linear Algebra - Concerned with vector spaces and linear mapping between such spaces.
- Logic - The principles of reasoning or arriving at some conclusion, though it is not logical, based on statements or propositions.
- A - B - C - D - E - F - G - H - I - J - K - L - M - N - O - P - Q - R - S - T - U - V - W - X - Y - Z
- Mathematical Analysis - Deals with limits and related theories, such as differential, integral , measure, infinite series, and analytic functions.
- Mathematical Constant - A special number that is significantly interesting in some way.
- Mathematical Optimization - The selection of the best element from some set of available alternatives.
- Mathematical Proof - Demonstrates that a statement is always true.
- Mathematical Statistics - The study of statistics from the standpoint of mathematics of analysis, collection, interpretation, presentation, and organization of data.
- A - B - C - D - E - F - G - H - I - J - K - L - M - N - O - P - Q - R - S - T - U - V - W - X - Y - Z
- Number - A mathematical object used to count.
- Number Theory - Deals with the properties of numbers and the relationships between them, primarily integers.
- Numeral System - A mathematical notification of a given set, using digits or other symbols in a consistent manner.
- A - B - C - D - E - F - G - H - I - J - K - L - M - N - O - P - Q - R - S - T - U - V - W - X - Y - Z
- Operation - A calculation from zero or more input values to an output value.
- Optimization - The process of maximizing or minimizing an objects function by finding the best avaliable values across a set of inputs.
- Order Theory - Deals with order using bionary relations.
- A - B - C - D - E - F - G - H - I - J - K - L - M - N - O - P - Q - R - S - T - U - V - W - X - Y - Z
- Plane Geometry - A two dimensional figure, also called planar geometry, with edges.
- Planck Constant - A physical constant that is the quantum of electromagnetic action, which relates the energy carried by a photon to its frequency.
- Probability - The study of change or the likelihood of an event happening.
- Proposition - A statement that is either true or false.
- Propositional Logic - A tool for reasoning about how various statements affect one another.
- Pure Mathematics - The study of mathematical concepts independently of any application outside matnematics.
- A - B - C - D - E - F - G - H - I - J - K - L - M - N - O - P - Q - R - S - T - U - V - W - X - Y - Z
- Scalar - A quantity that is fully described by its magnitude or size and is independent of any specific direction.
- Set Theory - Studies sets, which informally are collections of objects.
- Solid Geometry - A three-dimensional figure with connecting edges on multiple planes.
- Standard Deviation - A measure that is used to quantify the amount of variation or dispersion of a set of data values.
- Statistics - The study of analysis, collection, interpretation, presentation, and organization of data.
- Symmetry - An agreement in dimensions and arrangement.
- Symmetry Number - The number of different but indistinguishable or equivalent arrangements or views of the object.
- A - B - C - D - E - F - G - H - I - J - K - L - M - N - O - P - Q - R - S - T - U - V - W - X - Y - Z
- Topology - The spaces and their properties while under any continuous deformation.
- Trigonometry - The relations between the sides and angles of plane or spherical triangles.
- A - B - C - D - E - F - G - H - I - J - K - L - M - N - O - P - Q - R - S - T - U - V - W - X - Y - Z
- Vector - A mathematical entity that has both magnitude and direction.
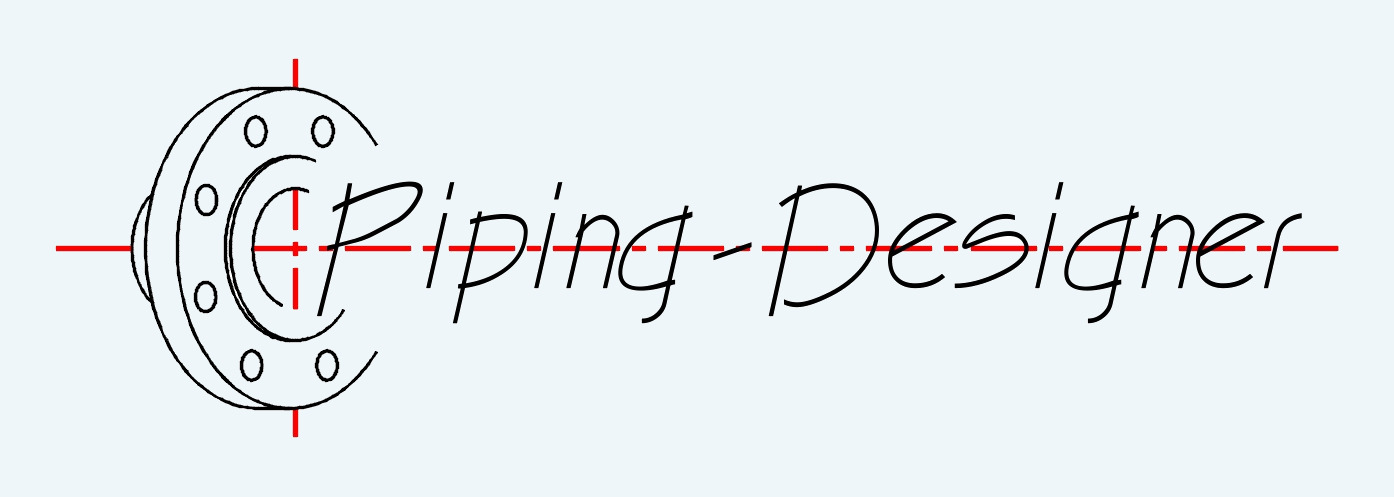
Read more
-
Physics Glossary
- A - B - C - D - E - F - G - H - I - J - K - L - M - N - O - P - Q - R - S - T - U - V - W - X - Y
- Angular Acceleration - Of an object is the rate at which the angle velocity changes with respect to time.
- Alternating Current - An electric current that reverses its direction over and over.
- Aerodynamics - How forces act on the way objects move through air.
- Acoustics - Studies the interactions of acustic waves with gas, liquid, and solid medias on a macro and micro level.
- Acceleration - The rate of change of velocity.
- Absolute Zero - The temperature at which all motion within molecules completely stops. Below absolute zero temperature does not exist. At this temperature nothing is in motion.
- Angular Displacement - The angle through which a body moves in a circular path.
- Angular Momentum - How much an object is rotating around a fixed point. The angular momentun of a body is equal to the mass of the body multiplied by the cross product of the position vector of the particle with its vertical velocity.
- Astrobiology - The search for life outside earth.
- Astrogeology - The geology of planets and their moons, astroids, comets, and meteorites.
- Astrometry - The percise measurement of where stars and other celestial bodies are positioned and move in space.
- Astronomy - Anything in the universe beyond earth.
- Astrophysics - The way our solar system and earth formed and the functions of planets and other celestrial bodies.
- Atmospheric Physics - The study of physics to the atmosphere; aerosols, clouds, and gasses, basically airborne particles, that surround the planetary bodies of the solar system.
- Atomic - The study of atoms as an isolated system of electrons and an atomic nucleus.
- Atomic Mass Unit - The unit of mass used to measure atoms and molecules.
- Atomic Number - Is equal to the number of protons in an atom's nucleus. The atomic number determines which element an atom is.
- Avogadro's Gas Law - When temperature and pressure are held constant, the volume of a gas is proportional to the number of moles of gas present.
- A - B - C - D - E - F - G - H - I - J - K - L - M - N - O - P - Q - R - S - T - U - V - W - X - Y
- Binding Energy - The energy required to break a nucleus into its constituent protons and neutrons or the energy equivalent released when a nucleus is formed.
- Biology (Biological) - The study of living organisms such as animals and plants.
- Biophysics - Studies the laws and principles in physics that describes patterns seen in biological systems.
- Black Hole - A point or extreme mass in spacetime with a radius, or event horizon, inside of which all electromagnetic radiation is trapped by gravety.
- Boyles Law - States that the volume occupied by a given mass of gas varies inversely with the absolute pressure if the temperature remains constant.
- Butterfly Effect - A name given to the extreme sensitivity of chaotic systems, in which small changes or disturbance lead to drastically different outcomes.
- A - B - C - D - E - F - G - H - I - J - K - L - M - N - O - P - Q - R - S - T - U - V - W - X - Y
- Chaos Theory - Deals with complex systems whose behavior is highly sensitive to slight change in conditions.
- Centrifugal Force - When a force pushes away from the center of a circle, but this does not really exist. When an object travels in a circle, the object always wants to go straight, but the centripetal force keeps the object traveling along an axis of rotation.
- Centripetal Force - The force that makes an object follow a curved path. Is a force generated when an object keeps traveling along a axis of rotation.
- Chemical Physics - The study of physics theories before modern physics.
- Chemistry (Chemical) - Uses techniques from atoms, molecular physics, and matter physics to study chemical processes from the point of view of physics.
- Classical - A division of physics that encompasses Classical Mechanics, Electromagnetism, Newton's Laws of Motion, and Thermodynamics.
- Classical Mechanics - The study of bodies in motion, including bodies that remain at rest.
- Climatology - Climate and how it changes over time.
- Condensation - A physical change of a substance from a gas phase to a liquid phase. Certain natural events cause condensation of water vapor in the atmosphere such as clouds, fog, and mist.
- Convection - Convection is the energy transfer of heat by air, water, or any other fluid to and object. It includes energy transferred by random molecular motion as well as energy transferred by the bulk motion of the fluid.
- Cosmology - The origin and eventual fate of the universe.
- Coulomb's Law - The magnitude of the electrostatic force between two electric charges.
- Current - The rate of flow of electricity in a circuit, measured in amperes.
- A - B - C - D - E - F - G - H - I - J - K - L - M - N - O - P - Q - R - S - T - U - V - W - X - Y
- Density - The ratio of the amount of matter in an object compared to its volume.
- Direct Current - An electric current that flows in only one direction.
- Displacement - The change in position.
- Dynamics - The relationships between different motions of objects and what affects them like force, mass, momentum and energy.
- A - B - C - D - E - F - G - H - I - J - K - L - M - N - O - P - Q - R - S - T - U - V - W - X - Y
- Econophysics - The economic system which are not subsets of energy and matter.
- Elasticity - Measures the stiffness of an elastic material. Elasticity can deform bodies and return to its original shape when the forces exerted are removed.
- Electric Field - An invisible space around a charged particle where an electric force is exerted on other charged particles, in tha same way as a magnetic field is the field of force that surrounds a magnet.
- Electrical Resistance - The property of opposing or reducing electric current.
- Electromagnetic Radiation - A wave that travels through space at the speed of light, consisting of an electrical field that periodically grows and dies, alternating with a magnetic field that periodically grows and dies.
- Electromagnetism - The basic forces of nature that determine the effect between energy and matter.
- Empirical - Refers to an approach or formula based on observation, experimentation, or real world data rather than deriving it from theoretical principles or first principles. Empirical models are developed by collecting and analyzing data to establish relationships between variables and make predictions or estimates.
- Energy - Never created or destroyed First Law of Thermodynamics, but it can be transferred from one object to another.
- Entropy - Measures the unavailable energy in a heat system.
- Escape Velocity - The minimum velocity required to leave a planet or moon or the minimum velocity to overcome the pull of gravity.
- A - B - C - D - E - F - G - H - I - J - K - L - M - N - O - P - Q - R - S - T - U - V - W - X - Y
- Field Theory - A theory that describes physical reality, including spacetime continuum, by means of the influence of a field, such as gravity on objects.
- Flowing Time - A view of spacetime that supports the truly temporal character of time as a fourth dimension and thus insists that flowing time is integral to the structure of reality.
- Fluid Dynamics - The motion in fluids for both liquids and gases.
- Force - The push or pull of an object resulting in a change from rest or motion.
- Freezing Point - The temperature at which a phase change of liquid to solid takes place.
- Friction - The mechanical resistance to the relative movement of two surfaces. The frictional force on each body is in an opposite direcrion to the motion of the other body.
- A - B - C - D - E - F - G - H - I - J - K - L - M - N - O - P - Q - R - S - T - U - V - W - X - Y
- Galaxy - A large collection of stars, gasses, and dust that are part of the universe bound togeather by gravitational forces.
- Gamma Ray - A form of electromagnetic radiation produced by some kinds of radioactive decay.
- Gas - Able to be compressed to fit a confined space and expanded when released.
- General Relativity - Space-time tells matter how to move, matter tells space-time how to curve.
- Geomagnetism - The origin and nature of the earth's magnetic field.
- Geophysics - The physical properties and dynamics of the earth and planets.
- Gravity - A force pulling togeather all matter.
- A - B - C - D - E - F - G - H - I - J - K - L - M - N - O - P - Q - R - S - T - U - V - W - X - Y
- Heat - A form of energy that causes physical change in what is being heated. The lack of heat is cold. This physical change comes from total amount of internal energy (kinetic energy and potential energy) possessed by an object or substance.
- Hydrodynamics - The motion of fluids and the way different forces affect their movement.
- Hydrology - The study of water in the environment.
- A - B - C - D - E - F - G - H - I - J - K - L - M - N - O - P - Q - R - S - T - U - V - W - X - Y
- Ice point - A transitional phase of a substance from a liquid to a solid.
- Internal Energy - The total of all energies associated with the motion of the molecules in the system.
- A - B - C - D - E - F - G - H - I - J - K - L - M - N - O - P - Q - R - S - T - U - V - W - X - Y
- Kinematics - Studies the trajectory of particles or bodies and does not take into account the mass of each particle in the system. Can be considered a branch of mathmatics.
- Kepler's First Law - The orbit of every planet is an ellipse with the sun at one of the two foci.
- Kepler's Second Law - A line joining a planet and the Sun sweeps out equal areas during equal intervals of time.
- Kepler's Third Law - The square of the orbital period of a planet is directly proportional to the cube of the semi-major axis of its orbit.
- Kinetic Energy - The energy in moving objects or mass. If it moves, it has kinetic energy.
- A - B - C - D - E - F - G - H - I - J - K - L - M - N - O - P - Q - R - S - T - U - V - W - X - Y
- Latent Heat - The energy absorbed or released by a substance during a constant temperature or phase change from a solid to liquid, liquid to gas or vise versa.
- Law of Conservation of Energy - States that energy cannot be created or destroyed, but may be changed from one form to another.
- Law of Conservation of Mass - States that matter can neither be created or destroyed. You can mix, separate or rearrange, but the total amount of mass remains the same.
- Law of Conservation of Matter - States that the mass of an object or collection of objects never changes over time, even when the matter changes form.
- Law of Conservation of Momentum - States that momentum only moves from one place to another, since it is neither created or destroyed.
- Light - The electromagnetic radiation of a wavelength that is visibal to the human eye. Light travels at a constant speed of about 300,000 kilometers per second.
- Light Year - The distance that light travels in one year, given that light travels at a constant speed of about 300,000 kilometers per second, works out to about 9,461,000,000,000 kilometers (5.879,000,000,000 miles).
- Longitudinal Stress - The stress imposed on the long axis of any shape. It can be either a compressive or tensile stress.
- A - B - C - D - E - F - G - H - I - J - K - L - M - N - O - P - Q - R - S - T - U - V - W - X - Y
- Magnetic Field - Magnetic fields never cross, never start or stop, where the field is strongest lines bunch togeather and can be seen clearly seen in the real world.
- Mass - The amount of matter an object has.
- Mathematical - Applies mathematical ideas to problems in physics or inspired by physics.
- Matter - When you look around, everything you see or may not see in the universe is made up of matter. If it has a mass and takes up space, it is matter.
- Meterology - A study of air polution, analysis and forcasting, atmospheric chemistry, atmospheric dynamics, climatology, global climate, meteorological instruments, and oceanography.
- Moment of Inertia - Measures the resists or change an object has to rotational acceleration about an axis.
- Momentum - The amount of mass in motion of an object.
- Motion - The acceleration, displacement, or velocity of an object relative to a given frame of reference.
- A - B - C - D - E - F - G - H - I - J - K - L - M - N - O - P - Q - R - S - T - U - V - W - X - Y
- Natural Selection - The process by which individuals' inherited needs and abilities are more or less closely matched to resources available in their evironment, giving those with greater fitness a better chance of survival and reproduction.
- Nuclear - Understand the properties of all different forms of nuclear matter.
- Nuclear Fission - The process by which an atomic nucleus splits into two or more large fragments of comparable mass, simuitaneously producing addititional neutrons and vast amounts of energy.
- Nuclear Fusion - The process by which two lighter atomic nuclei combine at extremely high temperatures to form a heavier nucleus and release vast amounts of energy.
- Nuclear Physics - Studies the building blocks and interactions of atomic nuclei.
- Nucleus - The center region of an atom where protons and neutrons are located.
- A - B - C - D - E - F - G - H - I - J - K - L - M - N - O - P - Q - R - S - T - U - V - W - X - Y
- Oceanography - The biological and physical condition of the ocean.
- Omega - Greek for ending or last.
- Optics - The properties and behavior of light and the reaction between energy, light, and matter.
- A - B - C - D - E - F - G - H - I - J - K - L - M - N - O - P - Q - R - S - T - U - V - W - X - Y
- Particle Physics - Understanding the basic forces of nature, like matter and radiation and their interaction.
- Physical Properties - These are the properties that are not mechanical properties, they are relate to the physics of a material such as thermal expansion, boiling point, color, ect.
- Plank Energy - The super-high energy (approximately \(1.22\;x\; 10^{19}\) GeV) at which gravity becomes comparable in strength to the other fundamental forces, and at which the quantum effects of gravity becomes important.
- Plank Length - The fantastically tiny length scale (approximately \(1.6\;x\; 10^{-35}\) meters) at which gravity becomes comparable in strength to the other fundamental forces.
- Plank Temperature - The temperature of the universe at 1 plank time after the big bang, approximately equal to \({1.4\;x\;10^{32} }\; {^\circ C} \).
- Plank Time - The time it would take a proton traveling at the speed of light to cross a distance equal to the plank length.
- Plasma - Plasma is the four phase of matter. It is everywhere in the universe and the most common of all matter. Of all types of matter it is closest to a gas.
- Plasma Physics - The study of plasma.
- Power - The rate of doing work or the rate of using energy per unit time.
- Pulsar - A highly-magnetized rapidly-rotating neutron star that sweeps regular pulses of intense electromagnetic radiation around space like a lighthouse.
- A - B - C - D - E - F - G - H - I - J - K - L - M - N - O - P - Q - R - S - T - U - V - W - X - Y
- Quantum - The study of how everything works at the molecular and smaller levels.
- Quantum Mechanics - Deals with atomic and sub-atomic particles.
- Quantum Physics - Deals with the physical phenomena, where the action is on the order of the Planck constant.
- A - B - C - D - E - F - G - H - I - J - K - L - M - N - O - P - Q - R - S - T - U - V - W - X - Y
- Redshift - The shifting of emitted electromagnetic radiation towards the less energetic red end of the electromagnetic spectrum when a light source is moving away from the observer.
- Relativity - The relationship between energy, matter, space, time, and velocity.
- A - B - C - D - E - F - G - H - I - J - K - L - M - N - O - P - Q - R - S - T - U - V - W - X - Y
- Saturated Air - Air in which equilibrium exists between evaporation and condensation. The relative humidity is 100 percent.
- Saturated Solution - The apparent limit to dissolving a given solid in a specified amount of water at a given temperature.
- Seismology - The study of seismic waves, earthquakes, and the mechanics of soil and rock materials.
- Shear Stress - Tends to deform the material by breaking rather than stretching without changing the volume by restraining the object.
- Solar Mass - The quantity equal to the mass of the sun.
- Solar System - A star and all the planets and other bodies that orbit it.
- Solid-state - Deals with the phisical properties of solids, especially in the electric and magnetic properties of solid crystalline materials like semiconductors.
- Sound and Oscillation - Sound is usally caused by the process in which energy is emitted as particles or waves from a soild vibrating surface or fluid disturbance.
- Space-time - Describes the fabric of reality. A conceptual model combining the three dimensions of space with the fourth dimension of time.
- Special Relativity - Motion warps space and time.
- Specific Heat - The amount of heat required to raise the temperature of a material 1 degree.
- Speed - The rate of change or distance with time. Speed is a scalar quantity having no direction. Speed is not velocity, they do not mean the same thing.
- Speed of Light - Travels at a speed of exactly 299,792,458 meters per second, or about 300,000 kilometers per second, a speed which remains constant irrespective of the speed of the source of the light or of the observer.
- Statistical Mechanics - Studies any physical system that has a large number of degrees of freedom.
- Stefan-Boltzmann Law - Describes the power radiated from a black body, an ideal black surface that absorbs all radiant energy falling on it, in terms of temperature.
- Stiffness - The resistance of the elastic deformation of an object that applies to both compression and tension.
- Sublimation - A physical change of a substance from a solid phase to a gas phase and does not pass through the transitional liquid phase.
- Sun - The closest star to earth and the center of out solar system.
- Supernova - A cataclysmic explosion caused by the collapse of an old massive star which has used up all its fuel.
- A - B - C - D - E - F - G - H - I - J - K - L - M - N - O - P - Q - R - S - T - U - V - W - X - Y
- Temperature - Normally described as the amount of heat or cold, but it is neither heat or cold.
- Thermal Expansion - The increase in length, area or volume due to the increase (in some cased decrease) in temperature.
- Thermodynamics - How heat relates to energy and work.
- Time - A measurement to define a continuous series of events.
- Time Dilation - The slowing of time in a frame of reference moving at nearly the speed of light relatives to an observer.
- A - B - C - D - E - F - G - H - I - J - K - L - M - N - O - P - Q - R - S - T - U - V - W - X - Y
- Uniform Acceleration - When the velocity of a body increases by equal amounts, in equal intervals of time.
- Uniform Speed - When a body travels an equal distance, in equal intervals of time.
- Uniform Velocity - When a body travels along a straight line in a particular direction and covers equal distances, in equal intervals of time.
- Universe - The total sum of all matter and energy that exists.
- A - B - C - D - E - F - G - H - I - J - K - L - M - N - O - P - Q - R - S - T - U - V - W - X - Y
- Velocity - The rate of change or displacement with time.
- Vibration - A back and forth motion that repeats itself.
- Volcanology - The activities and history of volcanos.
- A - B - C - D - E - F - G - H - I - J - K - L - M - N - O - P - Q - R - S - T - U - V - W - X - Y
- Weight - Weight is not mass. Weight is a force on an object accelerated by gravity.
- Work - The overcoming of resistance through space and is the measure of force x distance.
- White Hole - The theoretical time reversal of a black hole, which arises as a valid solution in general relativity.
- Wormhole - A hypothetical tunnel through spacetime that connects widely distant regions, thus providing a kind of short-cut through spacetime.
- A - B - C - D - E - F - G - H - I - J - K - L - M - N - O - P - Q - R - S - T - U - V - W - X - Y
- Young's Modulus - Measures the stiffness of an elastic material. The ratio of the longitudinal stress applied to a body or substance to the resulting longitudinal strain within the elastic limits.
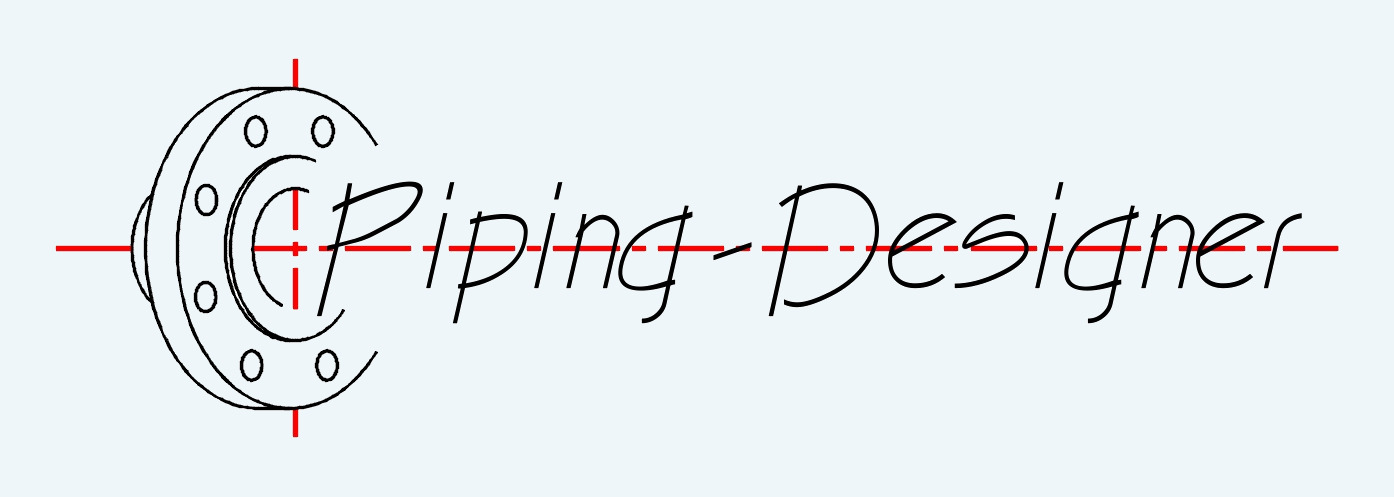
Read more
-
Bolt - Square, ANSI (in)
ASME Standards
Length (L) of a square bolt is measured from underside of head to the end of the bolt.

|

|
Bolt
Size
|
Body Diameter
D
|
Width Across Flat
A
|
Width Across Corner
B
|
Thickness
C
|
Max
|
Min
|
Basic
|
Max
|
Min
|
Max
|
Min
|
Basic
|
Max
|
Min
|
1/4
|
0.260
|
0.237
|
7/16
|
0.375
|
0.362
|
0.530
|
0.498
|
7/32
|
0.188
|
0.156
|
5/16
|
0.324
|
0.298
|
1/2
|
0.500
|
0.484
|
0.707
|
0.665
|
17/64
|
0.220
|
0.186
|
3/8
|
0.388
|
0.360
|
5/8
|
0.562
|
0.544
|
0.795
|
0.747
|
21/64
|
0.268
|
0.232
|
7/16
|
0.452
|
0.421
|
3/4
|
0.625
|
0.603
|
0.884
|
0.828
|
9/32
|
0.316
|
0.278
|
1/2
|
0.515
|
0.482
|
13/16
|
0.750
|
0.725
|
1.061
|
0.995
|
7/16
|
0.348
|
0.308
|
5/8
|
0.642
|
0.605
|
1
|
0.938
|
0.906
|
1.326
|
1.244
|
35/64
|
0.444
|
0.400
|
3/4
|
0.768
|
0.729
|
1 1/8
|
1.125
|
1.088
|
1.591
|
1.494
|
21/32
|
0.524
|
0.476
|
7/8
|
0.895
|
0.852
|
1 5/16
|
1.312
|
1.269
|
1.856
|
1.742
|
49/64
|
0.620
|
0.568
|
1
|
1.022
|
0.976
|
1 1/2
|
1.500
|
1.450
|
2.121
|
1.991
|
7/8
|
0.684
|
0.628
|
1 1/8
|
1.149
|
1.098
|
1 11/16
|
1.688
|
1.631
|
2.386
|
2.239
|
1
|
0.780
|
0.720
|
1 1/4
|
1.277
|
1.223
|
1 7/8
|
1.875
|
1.812
|
2.652
|
2.489
|
1 3/32
|
0.876
|
0.812
|
1 3/8
|
1.404
|
1.345
|
2 1/16
|
2.062
|
1.994
|
2.917
|
2.738
|
1 13/64
|
0.940
|
0.872
|
1 1/2
|
1.531
|
1.470
|
2 1/4
|
2.250
|
2.175
|
3.182
|
2.986
|
1 5/16
|
1.036
|
0.964
|
Read more
-
Square Nut (in)
Standard
- ASME Standards
- ASME B18.2.2 - Square and Hex Nuts
Square Nut (in) Datasheet
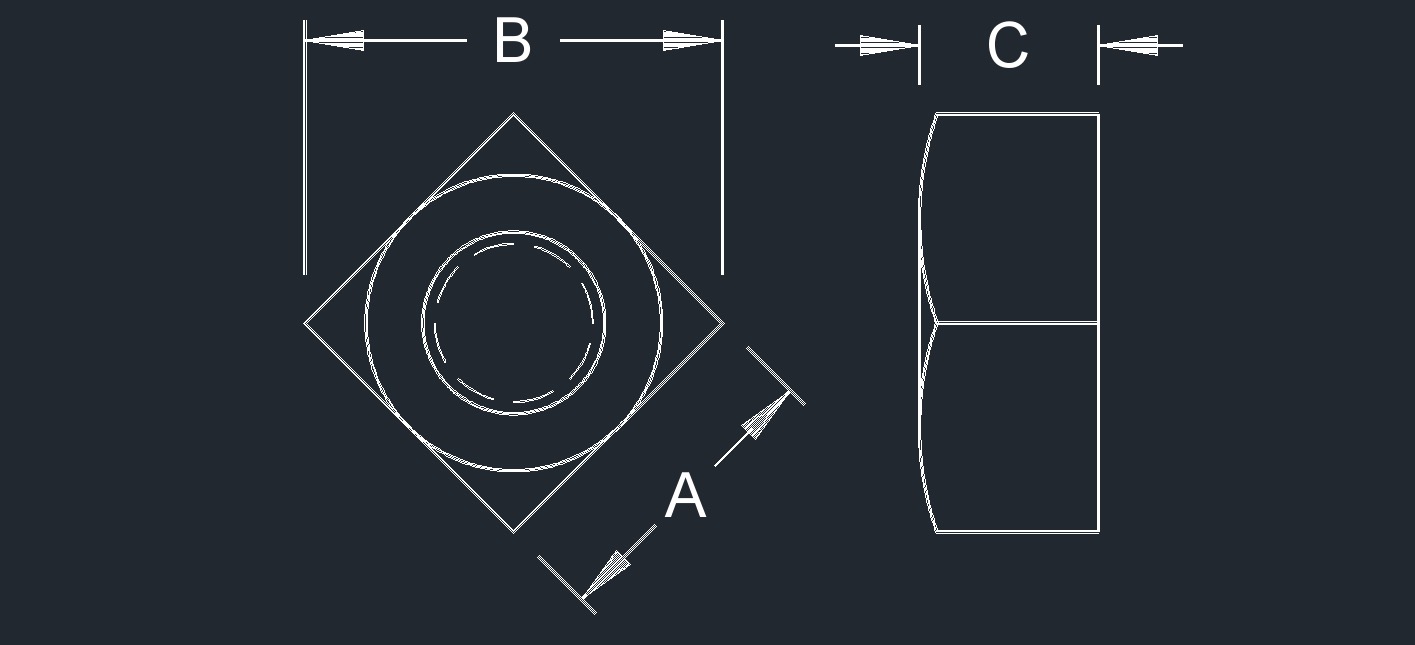
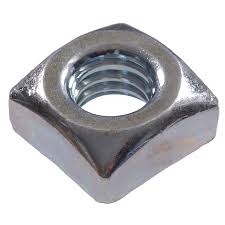
Bolt
Size
| Width Across Flat
A
| Width Across Corner
B
| Thickness
C
|
Basic | Max | Min | Max | Min | Basic | Max | Min |
1/4 |
7/16 |
0.438 |
0.428 |
0.619 |
0.554 |
7/32 |
0.235 |
0.203 |
5/16 |
1/2 |
0.500 |
0.489 |
0.795 |
0.721 |
17/64 |
0.283 |
0.249 |
3/8 |
5/8 |
0.625 |
0.606 |
0.884 |
0.802 |
21/64 |
0.346 |
0.310 |
1/2 |
13/16 |
0.812 |
0.788 |
1.149 |
1.052 |
7/16 |
0.458 |
0.418 |
5/8 |
1 |
1.000 |
0.969 |
1.414 |
1.300 |
35/64 |
0.569 |
0.525 |
3/4 |
1 1/8 |
1.125 |
1.088 |
1.591 |
1.464 |
21/32 |
0.680 |
0.632 |
7/8 |
1 5/16 |
1.312 |
1.269 |
1.856 |
1.712 |
49/64 |
0.792 |
0.740 |
1 |
1 1/2 |
1.500 |
1.450 |
2.121 |
1.961 |
7/8 |
0.903 |
0.847 |
1 1/8 |
1 11/16 |
1.688 |
1.631 |
2.386 |
2.209 |
1 |
1.030 |
0.970 |
1 1/4 |
1 7/8 |
1.875 |
1.812 |
2.652 |
2.458 |
1 3/32 |
1.126 |
1.062 |
1 3/8 |
2 1/16 |
2.062 |
1.994 |
2.917 |
2.708 |
1 13/64 |
1.237 |
1.169 |
1 1/2 |
2 1/4 |
2.250 |
2.175 |
3.182 |
2.956 |
1 5/16 |
1.348 |
1.276 |
Read more
Butterfly Valve Advantages and Disadvantages
|
Advantages | Disadvantages |
- Easy to install.
- The installation costs are low.
- Simple structure, small volume and light weight.
- The opening and closing time is short and the flow resistance is small.
- The opening and closing torque is small, because the butterfly plates on both sides of the rotating shaft are basically equal to each other under the action of medium, and the direction of torque is opposite, so it is easier to open and close.
- When the valve seat is fully open, the effective flow area of the valve seat channel is large and the fluid resistance is small.
- The sealing surface materials are generally rubber and plastic, so the low-pressure sealing performance is good.
- It can be used for media with suspended solid particles, and can also be used for powdery and granular media, depending on the strength of the sealing surface.
- It can be applied to the two-way opening and closing and adjustment of ventilation and dust removal pipelines.
- Widely used in pipelines, waterways, light industry, and petrochemical systems.
- Butterfly valves can transfer mud with a little fluid deposit in the outlet of the pipe.
|
- The flow adjustment range is small. When the opening is up to 30%, the flow rate will be nearly 95% or more.
- Due to the limitation of the structure and the sealing material, butterfly valve is not suitable for use in high temperature and pressure piping systems.
- The sealing performance is relatively poor compared to ball valves and globe valves, so it is not used for sealing requirements.
- Prone to cavitation at lower flows.
- When butterfly valves are used, throttling is limited to low pressure drop systems.
- A part of the butterfly disc is always facing the flow, even if it’s completely open.
|
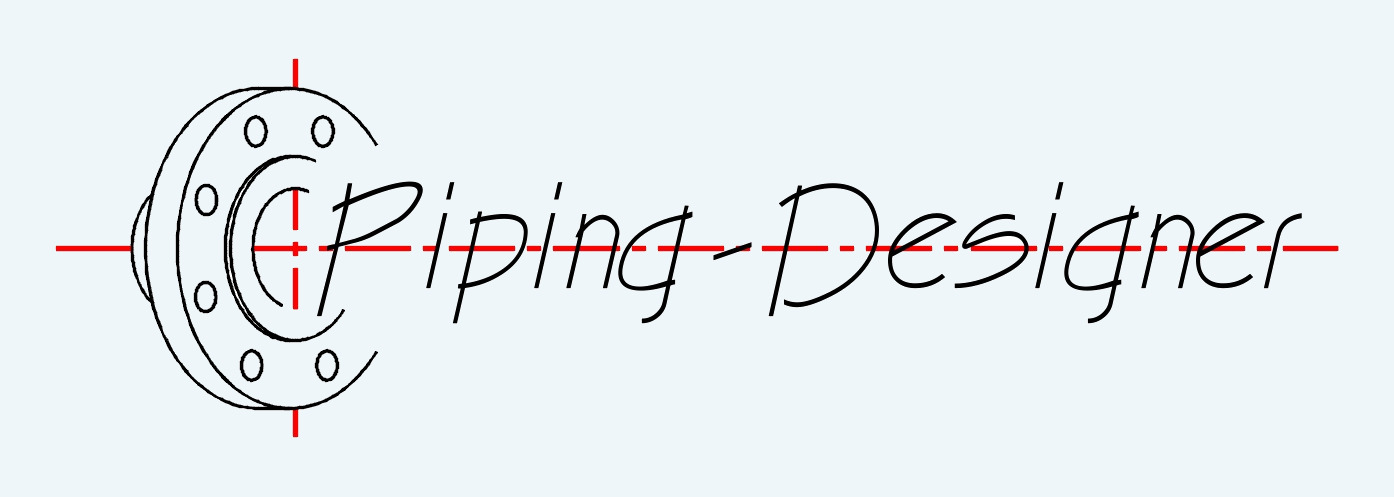